share
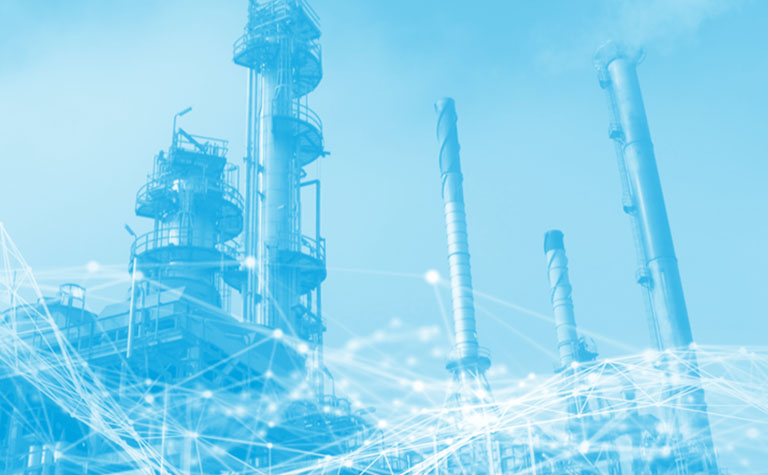
AT&T’s connectivity supports Howden Uptime for customers around the world
Global network enables the capture of information to schedule maintenance for business-critical machinery
Workers deep underground rely on surface-based machinery to deliver clean air and remove harmful gases from the site, sometimes more than a mile below the earth. AT&T* is providing global IoT connectivity to Howden Group Ltd.+ to deliver near real-time data from the business-critical heavy machinery that gets the job done.
‘Howden Uptime’ with AT&T global connectivity will allow the engineering company to track performance of its rotating equipment such as fans, compressors, steam turbines and heaters that cover industries from power generation, petrochemical, waste water, mining and cement, to a vast array of other industrial applications – anywhere around the world. With health and safety of employees a prime concern, alongside production efficiency, ensuring machinery is maintained effectively minimises the potential for unplanned downtime.
AT&T’s Global SIM and connectivity is part of the ‘Howden Uptime’ solution, a proprietary system using sensor technology to capture data from equipment installed at a customer’s site. It’s then sent to the cloud where a data analytics engine is used to schedule pro-active and reactive maintenance services, as well as equipment performance management.
Howden’s sensors and the communications module can be installed without any modifications to the existing plant infrastructure. The data gathered by Howden Uptime is continuously relayed to its in-house experts for analysis. As an equipment manufacturer with more than 160 years’ experience, Howden can translate the data to provide valuable advice and recommendations for action.
The digital twin is at the centre of the Howden Uptime solution. Using physics data on how equipment operates and responds to the environment, as well as information from sensors, the digital twin is used to analyse and simulate real world conditions. This includes how it responds to changes, and how Howden’s customers can improve their operations.
The data from Howden Uptime is used to provide automated predictive alerts, delivered, when necessary. Howden customers have access, via a secure portal, to current manuals, drawings, and reports, and Howden’s worldwide service network enables them to have local engineers on-site quickly to provide additional support.
Howden uses AT&T’s Global SIM and advanced satellite connectivity to transmit data from customers’ equipment and deliver performance optimization on demand. AT&T satellite services provide redundancy and virtually eliminate any coverage gaps.
“The technology stack that we built behind Howden Uptime is a cloud solution that uses one of the most advanced industrial IoT platforms,” says David Simpson, CIO, Howden Group Ltd. “And the connectivity piece with AT&T allowed us to come up with a highly secure cloud solution. It helps our customers operate efficiently and avoid unplanned outages.”
Howden also welcomed AT&T’s ability to provide technical guidance. “The world of connectivity and particularly the world of satellites are areas in which Howden doesn’t specialise,” adds Simpson. “Therefore, we’re very dependent on suppliers to provide us with guidance, observations and options. And AT&T is clearly a company that could do it across the standard SIM technology but also, and more importantly, on the satellite connectivity. And that was a key differentiator.”
“This is another example of the strength and global reach of the AT&T network,” said John Vladimir Slamecka, AT&T region president, EMEA. “By connecting Howden’s machinery to the cloud via our network, they can get near real-time information on how the equipment is performing and send engineers to make proactive repairs when they see a component is not working as it should.”
PR Archives: Latest, By Company, By Date